Installation
Well. this shouldn’t be our duty as those are 3rd party sensors, but as it is a common request, these are the general rules:
- Some lambdas (Innovate and UEGO) have a “output-” which must be connected to GND at the controller side (not the DAQ side), check the first picture.
- Connect output+ and output- to pin4 and pin 5 of the 6-pin connectors to DAQ: SP1, SP1+, SP3, SP5 (for Lambda 1 or Lambda 2 depending on the connector) (second picture). For SP4 and SP6 there are specific screw-connectors with the AN1 and AN2 labels.
- Power: of course it is always external, you can use a battery or a 12V power supply
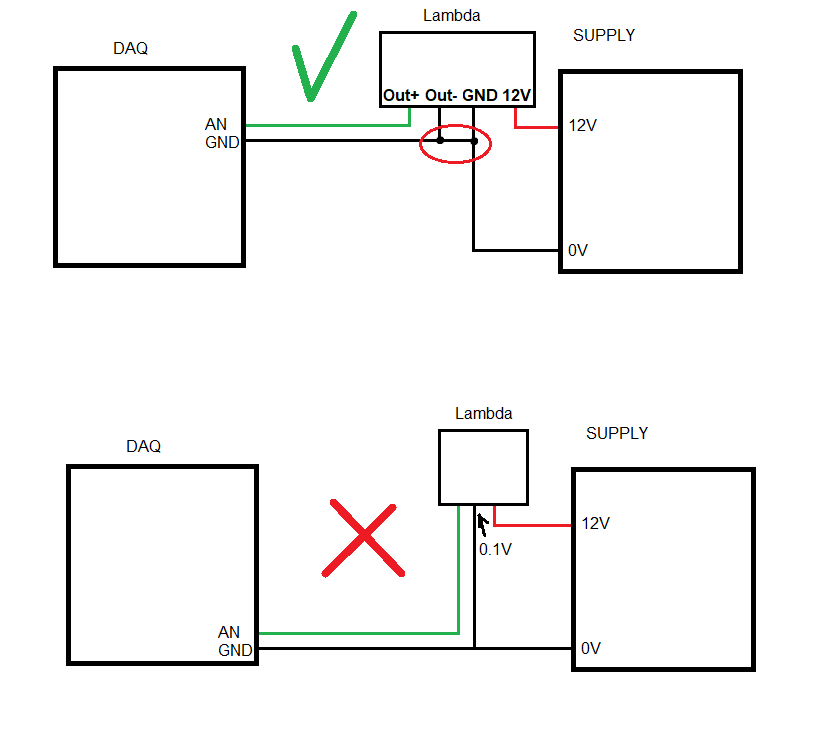
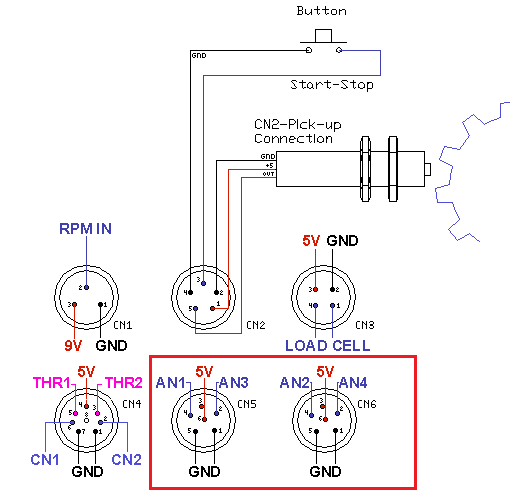
Calibration of loadcell, for dyno running with SportDevices SP1+, SP3, SP4, SP5 and SP6 DAQ units.
Procedure may be different depending on how the dyno is constructed. In this description there is use “calibration bar” and “Calibration weight”.
The purpose of calibrating the load cell is because the load cell normally is the most important factor in HP / TQ calculations in most dyno software.
Brake Torque is converted to linear force into the load cell thanks to balljoints and the physical position of the cell with respect the brake axle (load cell lever). This force is
converted to real-time data. Therefore, it is extremely important to perform this part of the dyno calibration 100% correctly.
An incorrectly calibrated loadcell will give incorrect dyno readings !!
It is recommended to do calibration, on a regular basis. As part of normal service on your dyno.
The load bar length is measured from the center of the brake shaft to the center of the calibration weight. The location of the loadcell has no significance with this method. The
software will automatically calculate the correct calibration factor.
A calibration weight is an important tool, and should therefore be stored and treated as an every important measuring tool.
The weight you should choose must be based on what max weight the load cell is nominated for and the length of the bar.
The purpose is to apply so much of the max load to the load cell, to get a better calibration.
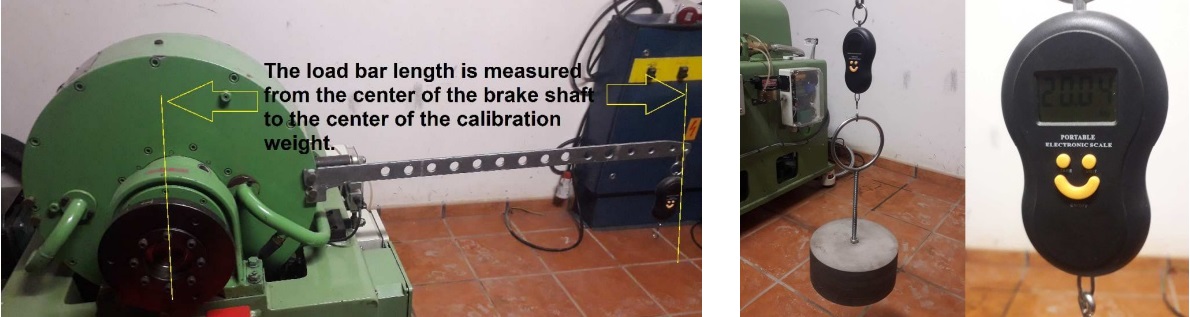
Step 1:
Open Loadcell Wizard and mount your cabling bar (Without weight on the bar).
The weight of the bar does not matter at this time. And will be offset at the end of calibration.
Zeroing:
- SP1+, SP5, SP6: The “zero setting” shouldn’t be used with these DAQs. Nevertheless, it is necessary to (re)Start the DAQ to execute the zeroing process cancels the bar’s weight
- SP3 and SP4: As those (old) DAQs do not perform the internal zeroing at startup, thus it is necessary to use the “Set to Zero” button.
Step 2:
Enter the Cabling bar length value (say 270 mm) and the calibration weight value (say 20 kg)
The next step is to place your calibrating weight on the bar. And then press “Calibration”
After the calibration the calibration weight and bar must be removed and the zero performed again:
- SP1+, SP5, SP6: restart the DAQ so the new (negative) offset is cancelled.
- SP3 and SP4: go back to “Step 1” and press “Set to Zero” again. This makes the offset for the calibration bar weight.
Go back to Step 2 and press “Ok”, calibration is now complete and stored on your computer
Alternative Calibration Methods (Depends on the dyno)
Some dynamometers can have a dedicated place at the same position that the load cell to perform the calibration directly over the cell. In these cases, the calibration bar length is the same than the load cell lever. If load cell lever (distance from axle to cell is 300 mm, calibration bar = 300 mm)
These methods have the advantage that do not use a physical calibration bar that adds a weight when installed in the brake (and subtract a weight offset when removed from the brake)
P.I.D. coefficients determine the brake response to the difference between the desired speed (target) and the current speed (this difference is called error).
The DAQ (SP1+ / SP5 / SP6) implements a standard PID, with I constant proportionally to P (Kp) Ti, this allows changing only Kp constant and SP5 will modify Ki to keep the same dynamic behavior. (Ki = Kp * 1 / Ti)
The DAQ does not implement a Kd derivative constant, but it implements a more sophisticated overshoot control.
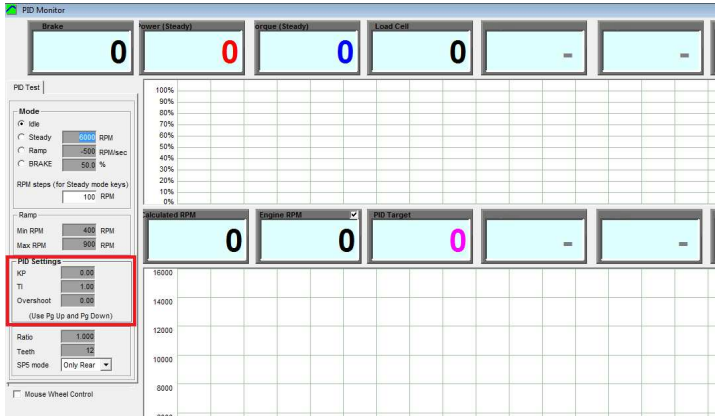
A good starting point for PID setup is:
Kp = 1-40 (1 to 5 for engine, hub and motorcycle dynos, 5 to 10 for car dynos with small rollers, and up to 40 for big rollers)
Ti = 1 (0.5 to 1.0)
TD = 0
- Kp basically controls the reaction time. Control can be made faster increasing Kp, but excessively high values will cause fast oscillations on the system, thus a balance has to be found between speed response and stability.
Kp by itself cannot make the speed control to reach the exact target speed, for this reason the integral control (I) is used. - Ti is (normally) modified in a narrow interval (typically 0.5 to 1.5). A low Ti will provide a faster approaching / drift to the target, specially in steady mode. But a low Ti will decrease the reaction speed (specially for ramp mode)
- Td: is a setting which tries to damp the reaction of the dyno .Normally with roller dynos inertia is high enough and Td is not used. Only lightweight dynos may need the Td setting., but up to cerain level (in steps 0f 0.01) in which the reaction starts to increase the high speed oscillations.
- Accel Filter: when using the Td setting set the “accel filter” to 1 to improve the calculation of the acceleration internal channel
Note: Since the addition of current-closed-loop to the Brake Power Supplies (PWS1.5, PWS3.x, HS-PWS) the reaction time of the system has been improved a lot.
Each power supply comes with 3 inputs: PWM (2 pins), CAN (4 pins) and Analog / Potentiometer (3 pins). In general only one can be used at a time for the speed control (PWM or CAN), with the exception of a safety potentiometer or brake pedal that can work in parallel as a safety control (only when it is necessary a rough braking)
Note that SP1+ and old SP4 have only PWM output, while SP5 and SP6 have also a CAN bus.
Advantages of PWM (for one or two brakes):
- There is a direct relationship between the DAQ output with the function in the Power Supply. Front rolller connector will always output the PWM for front Brake, and Rear Roller Connector will always output the PWM for rear Brake. No possible confusion (if cables are traced)
- It is not affected by interferences or collision between several modules. Each PWM line is only point to point
Disadvantages of PWM / advantages of CAN
- There is no feedback in PWM. CAN is more useful for 2-HUB, AWD and 4-HUB dynos as the SW can receive the feedback of each power supply before starting the test, and can record all telemetry (current and temperature) of each power supply to be stored with the tests as potential diagnosis in case something is wrong
- CAN allows to perform a Brake Resistance Measurement from the software
- PWM can have problems if many PWS have to be connected in parallel as the optocouplers take some power of the PWM line, while PWS provide a protocol for CAN to have the same CAN ID (for receiving commands) and different ID for telemetry. In this way a SP6 could control up to 16 x PWS, max 4 per channel
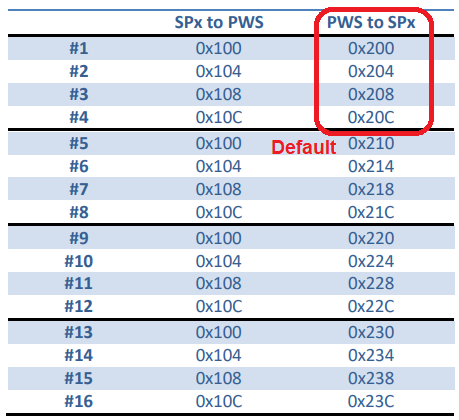
Connection:
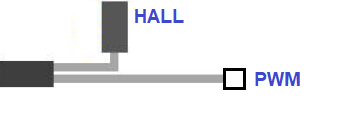
- PWM: SP1+, SP5 and SP6 include the PWM line in the 4th pin of the 5-pin connector (roller connector). Each Power Supply include a “Y” cable that splits this line and GND for the PWM, and provides another 5-pin connector for the hall sensor cable. Note that in the hall sensor+switch cable the pin 4 is used as GND (mainly for SP1), this is only possible when connecting the hall sensor + ext. cable to the output of the “Y” cable, not directly to the SP1+/SP5/SP6 output
- CAN: SP5 and SP6 provide a round 8-pin connector (GX-16) with CANH and CANL lines, and also GND and 5V (note that from PWS3.3 5V is no longer necessary from the DAQ, as it is obtained through a DC/DC in the same PWS). When more than one PWS is going to be used, the 4-pin connector in the PWS has to be chained to reach all of them
Terminators:
SP5 and SP6 include a terminator inside the PCB. Also, the last PWS in the chain must have the terminator jumper SET while the intermediate PWS will have them disabled.
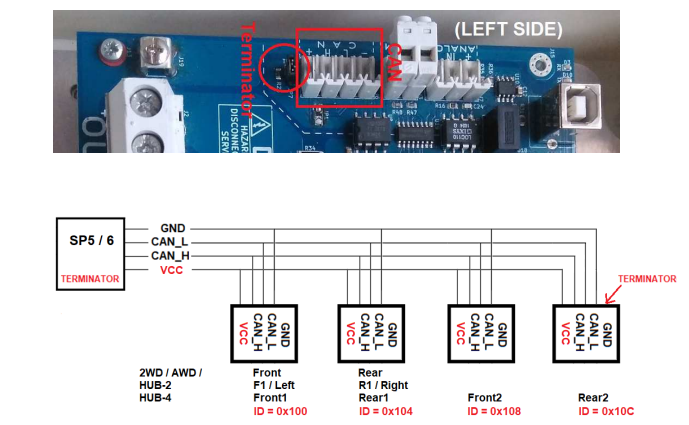
MSCOMCTL.OCX and SPView41.OCX errors
A few customers reported errors when installing the Software at the point when the installer is registring some OCX controls. For instance the MSCOMCTL.OCX there are two versions, in old Sportdyno V3.5 we used the version (6.01.9782) where in current Sportdyno versions we use a more recent version (6.01.9846) and for some reason this causes issues in some computers. A similar error can be shown when registring the SPVIEW41.OCX control
A temporary fix for this error, until we discover why some (few) computers show this error, is just installing the old Sportdyno V3.5 and then installing the latest Sportdyno V4.1.x versions, then the installation is successfull
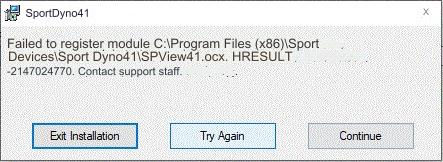
Something that causes many misunderstandings to new users regarding the SP1 configuration is the confguration of number of teeth and prescaler due to the fact that the SP1 does not syncrhonize these settings with the PC (the SP1 will not send this information during the connection process and then the PC will not be able to synchronize it). Then it is necessary:
- Ensure that the connection between the PC and the SP1 is established before configure these settings
- Configure the Number of Teeth and prescaler. For our stock gear it is Teeth=16 and Prescaler=1 (in most cases). Note that this configuration is only valid for rollers over 320 mm and max speed below 225 km/h! (max roller speed 3750 rpm). For higher speeds use the “auto” setting, which will set the prescaler to 4 to avoid problems. Please check the table below
- Press the “disquette” button, or press OK and reply “YES” to the question “do you want to send the new settings?”
- Verify that the SP1 LCD shows the stored value (this lasts only 2 or 3 seconds)
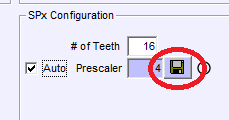
** Note: we are testing a new firmware which implements the same synchronization as SP1+, SP5 and SP6. This FW could be used in all SP1 V4 units
AUTOMATIC Prescaler Selection:
When the “auto” setting is ON, the software will select
- Teeth: 1 to 12: prescaler = 1
- Teeth: 13 to 49: prescaler = 4 (note that for our stock 16T gear it will chose prescaler=4, which can reduce the accuracy at low speeds)
- Teeth: 50 or more: prescaler = 16
Manual Prescaler Selection
In general when SP1 is used with our stock 16T gear, number of Teeth = 16 and prescaler = 1, but only for rollers over 320 mm diameter and top speed below 225 km/h. For lower diameters or higher speeds prescaler should be 4
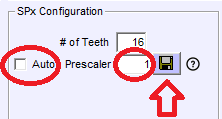
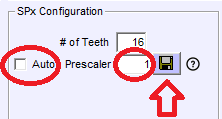
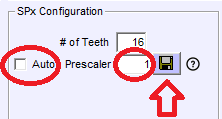
As maximum SP1 input is 1000 pulses per second, the user should ensure that the top frequency is not overpassed using the following formula:
Max Freq = Max Roller RPM / 60 * Teeth / prescaler
(Max Roller RPM = Max Speed (km/h) / 3.6 / (diameter_mm / 1000) * 3.1416) * 60)
Example:
For instance for a 320 mm roller running Max Roller RPM at 225 km/h is: Max Roller RPM = 225 / 3.6 / (0.320 * 3.1416) * 60 = 3730 RPM
And for 16T and prescaler = 1 Max Freq = 3730 / 60 * 16 / 1 = 994 Hz
Then for higher speeds (over 225 kmh) or lower roller diameters (below 320 mm) the prescaler should be 4 as in the automatic mode.
For the rest of combinations, say teeth 80 normally there is no need to do any calculation. The 16T is a little more problematic because it is in the border between prescaler=1 and prescaler=4, but it was selected as stock gear because it provides more pulses for the braked dynamometers.
Dyno Usage
The Capacitive Clamp (Red) (CAP-1) is envisaged to be used mainly on spark cables (High Voltage from coil to the spark). It senses the High Voltage peaks and sends them to the DAQ. In general it is good for single cylinder engines,
Drawbacks: it may get random pulses from other cylinders
There is also a variant (CAP-3) with a blue cable and the 3-pin connector which includes the amplifier circuit in the same clamp, this allows to make the sensing circuit less sensitive and focus only on the near ignition sources, which improves a little its performance on multi cylinder engines. This clamp is provided by default with the SP6 as it only has the 3-pin input
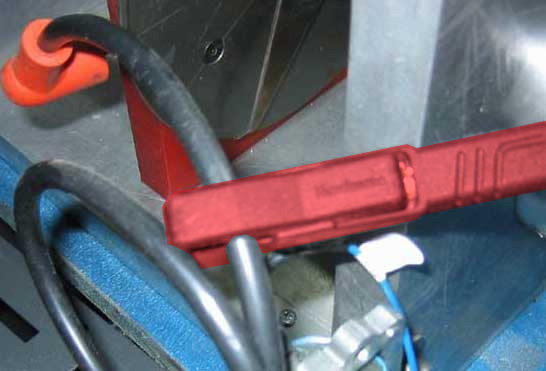
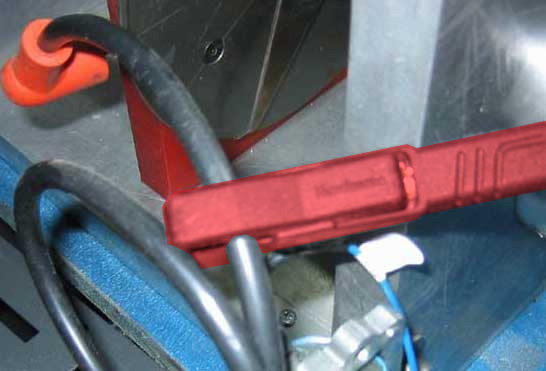
Inductive Clamp (black) (IND-3)
The inductive clamp senses the Current pulses (not voltage) and it is provided mainly to sense the current at ONE of the wires that go to the coil, specially for over-spark coils (as there is no spark cable!).
- In motorcycles typically there are two cables going to the coil, please set the clamp at ONE of the cables. Note that the clamp is sensitive to one direction but less to the other.
- In cars typically we have three cables going to the “amplified coil”, one of the cables is GND, the other is 12V and the other is the low power activation. As it is the coil who amplifies the signal and creates the current pulses, only the GND and 12V cables will have a pulses of current (use the clamp on ONE of them). The signal cable could even have almost Zero current, as normally these coils use an IGBT (its conductivity based on gate’s voltage, not current)
Current model:


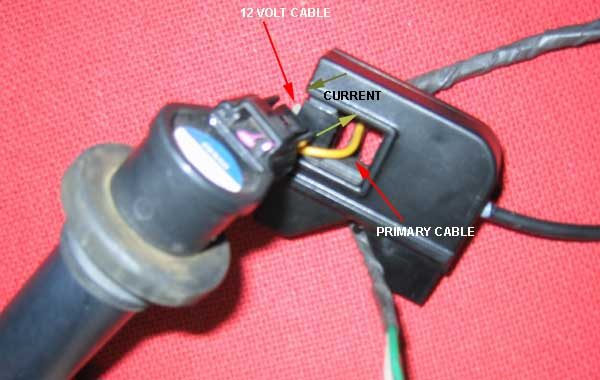
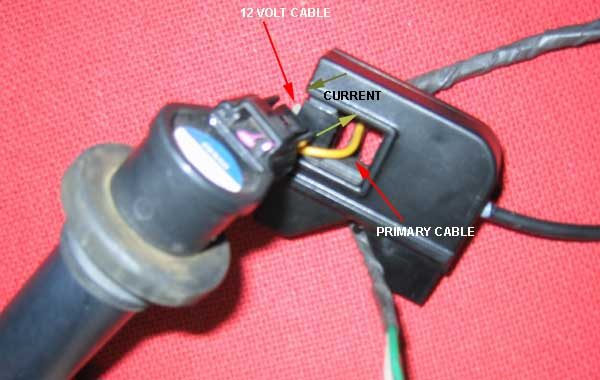
Drawbacks: mnany engines work in a “wasted-spark” schema to simplify the timing (one spark per turn). This means that they do one spark at compression-combustion stroke, but also a spark in exhaust stroke. This spark at exhaust stroke has no impact over the engine performance, but as the pressure is lower than during the combustion the sparks tend to be weaker (it is necessary less voltage to jump the spark gap than when working at a high pressure). This causes that the pulses sensed at the clamp are alternatively high and low, high and low, but also not at a constant level, but the weak pulse may sometimes overpass the activation level, and other times may not. Which will lead to show alternatively the value “RPM”, and “RPM / 2” in the gauges and the graphs
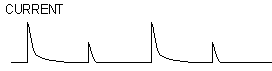
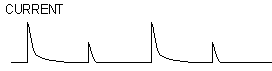
And when the engine decelerates as the amount of air-fuel mixture is very low in the chamber, even the compression phase may show 0 RPM as in the graph below, although this normally happens during a short time as the engine reaches the idling speed quite fast (Neutral Gear or Clutch have to be active to do the coast down test)
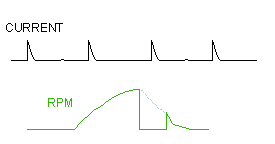
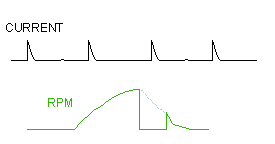
CVTs normally consist of a set of two pulleys that can change their width and a belt that can travel from a closer position in the drive pulley (and a more open position in the driven pulley) which works as a first gear, to a wider position in the drive pulley as the drive pulley becomes compressed (by centrifugal rollers or other mechanisms) which work as a high gear. An important feature of CVTs is that it exists infinite positions between the “low” position to the “high” position, which gives also multiple combinations for the ratio value which change during the test, thus it is NOT possible to perform a standard ratio calibration for CVTs.
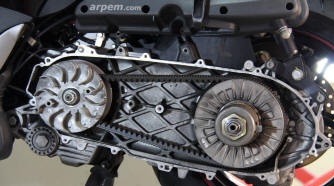
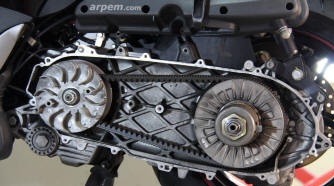
There are two ways to test a vehicle with a CVT (Continuous Variable Transmission)
Testing the CVT on its normal way of operation.
- Set Fixed Ratio = 1.000 (as the ratio changes during the whole acceleration phase) and
- use the starting and ending points referenced to speed. Note that it is also possible to start from a standstill either using manual start or setting the starting speed to 1 km/h
- The resulting test should be displayed as HP (wheel) vs Speed.
- Aux Torque can be used to get the Linear Force (thrust), but not ETQ
- Remarks:
- It is not possible to get the engine HP and the graphs vs actual the RPM (and makes not much sense). As the clutch is centrifugal in most cases the only way to disengage it is LIFTING the wheel and blocking the wheel, but this is a complicated and risky maneouver
- Also, it is not possible to get the actual engine TQ, it is better to use the second method (blocked CVT)


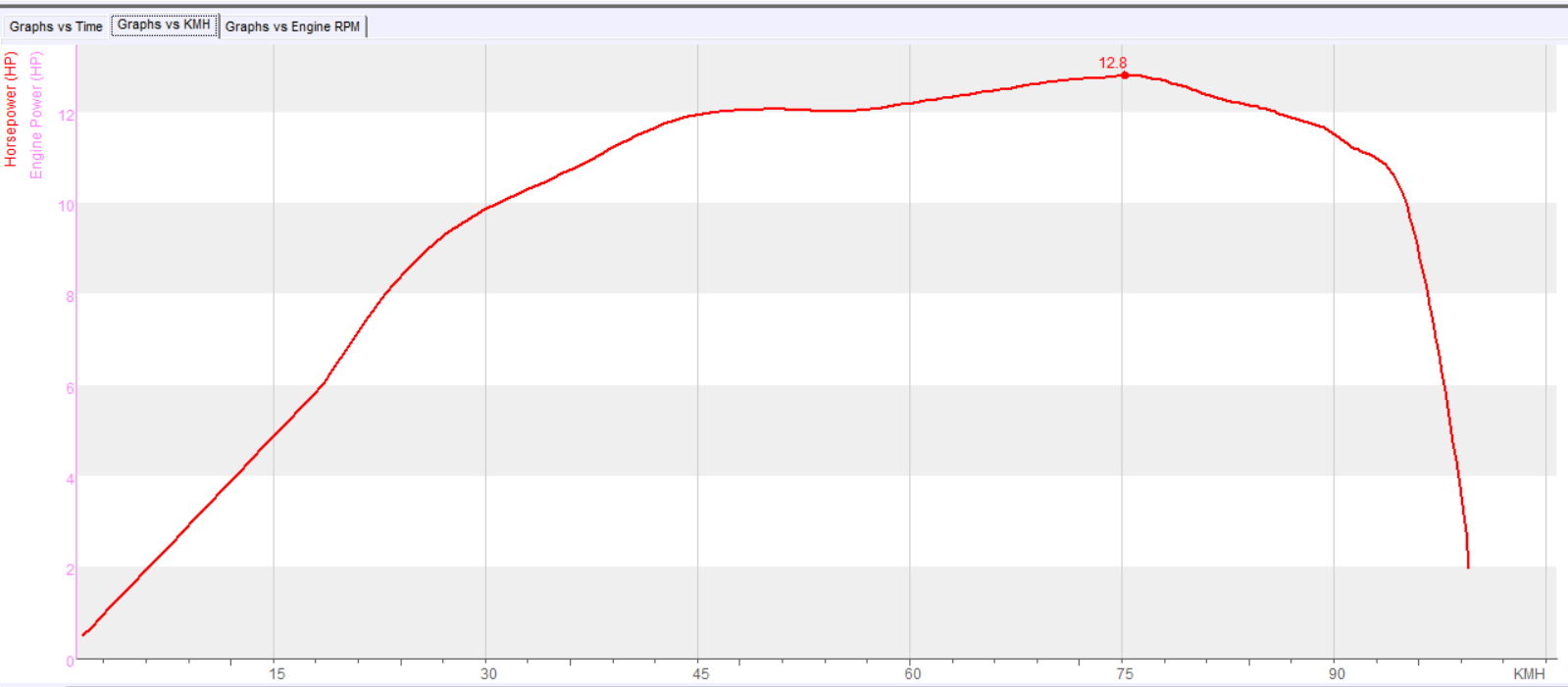
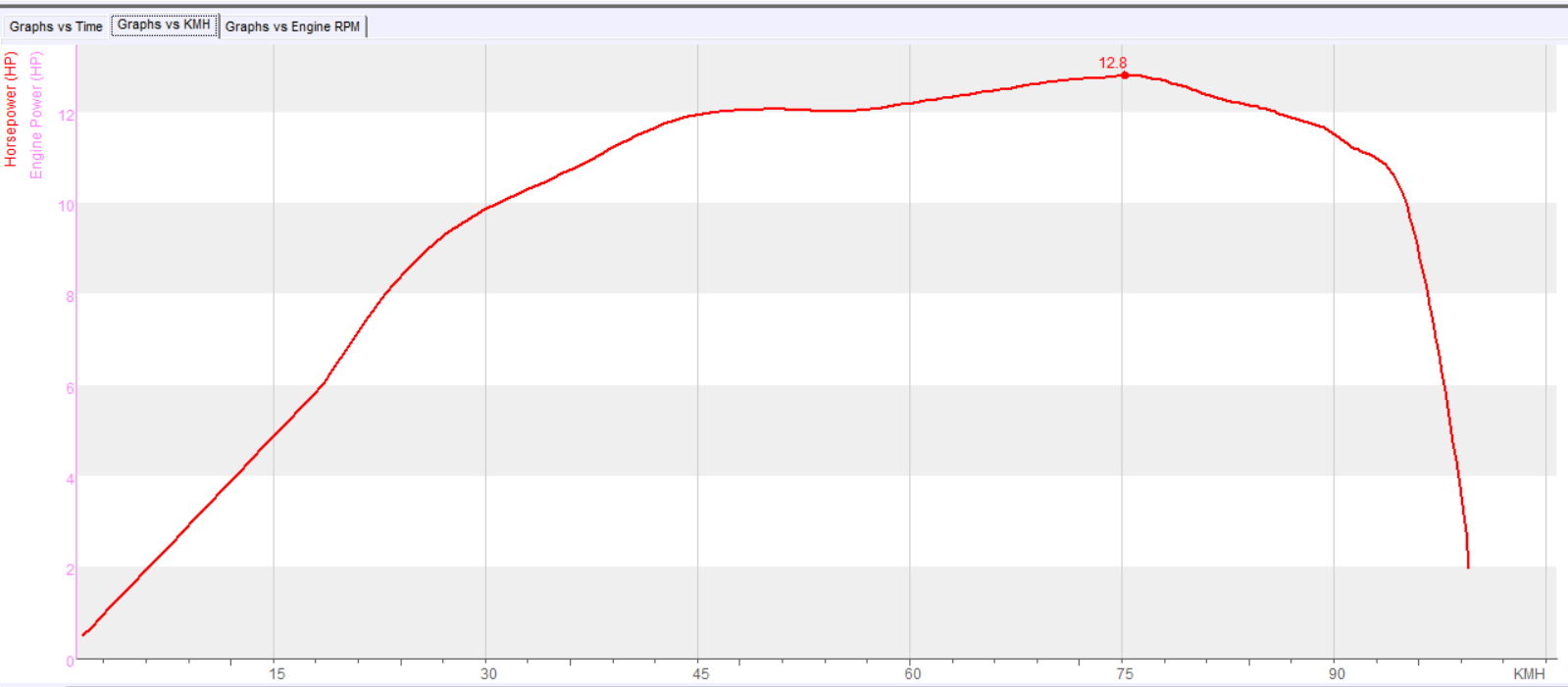
Testing the CVT with the pulley blocked in the “high gear”
This is the method to get the most information from the Engine, almost the same as a vehicle with a manual gearbox (with the limitation of the centrifugal clutch)
- Depending on the type of CVT, the pulley with the rollers may be set in a fixed position using washers, then the CVT will act as a fixed gear (high gear)
- When this modification has been performed, it is necessary to start the engine carefully as the clutch will start the vehicle in the high gear. The recording at full throttle shouldn’t start until the clutch is totally engaged. For instance if the vehicle normally gets the clutch totally engaged at 15 km/h, it is possible that with this modification this happens at 30 km/h
- When a test is recorded in this way, WHP and ETQ (uncorrected) channels are available vs actual Engine RPM, but EHP and corrected TQ are still not available due to the fact that the cetrifugal clutch is quite complex to be disengaged at top speed.
Displaying graphs vs actual Engine RPM
The X-Y graph can be used to display the graphs vs actual RPM (if the Engine RPM channel has enough quality), but in our opinion the resulting graph can be very confusing compared with the graphs-vs-speed, because indeed the purpose of the CVT is to keep the RPM almost constant during the widest (speed) range as possible
Press CTRL+F3 to enter the X-Y graph, and choose the 0x31-Engine RPM for the X axis
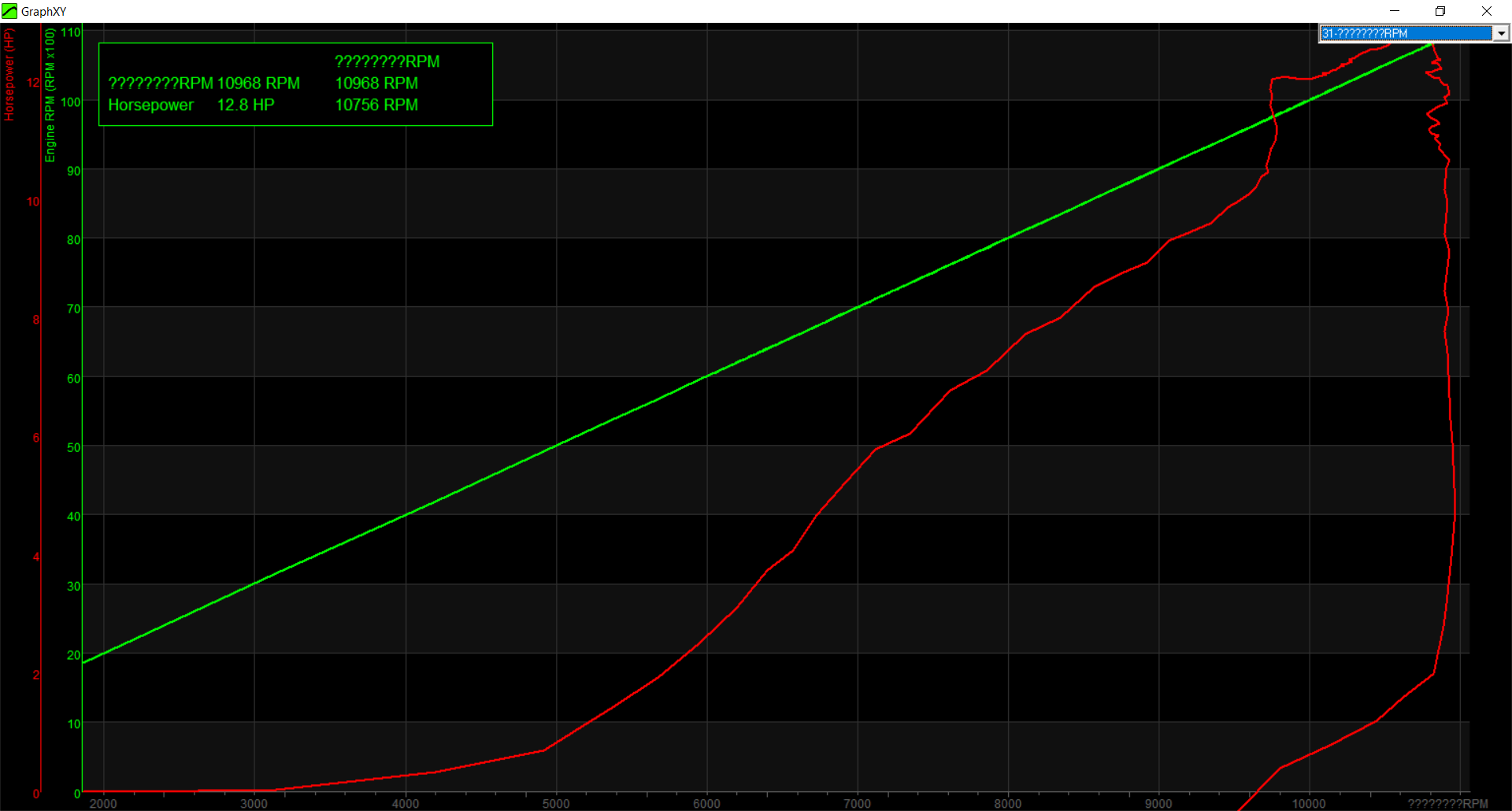
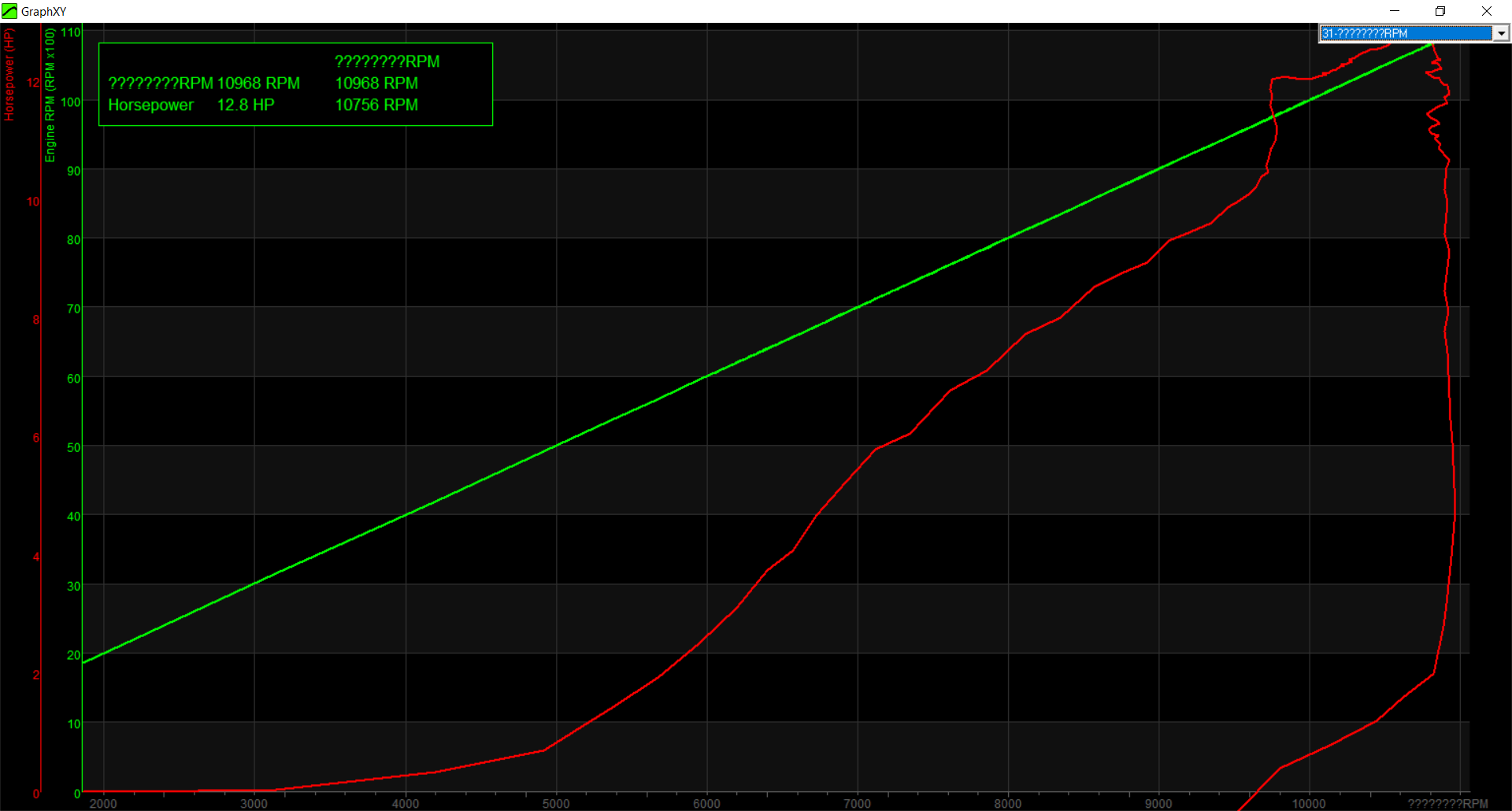
In an inertial dyno RAW power (power observed at rollers) is basically the same as the Wheel power (power that is available at wheels), with the only exception of the power lost at bearings, which can be ignored.
But in a braked dyno using air-cooled eddy current brakes, part of the power is used in the air-pump work in the brake rotors, specially for roller/brake speeds over 2000 RPM.
Solution:
The power wasted by the brake in the air-pump effect could me measured doing a high speed coast down test, but this is a complicated test due to the speeds and power levels involved.
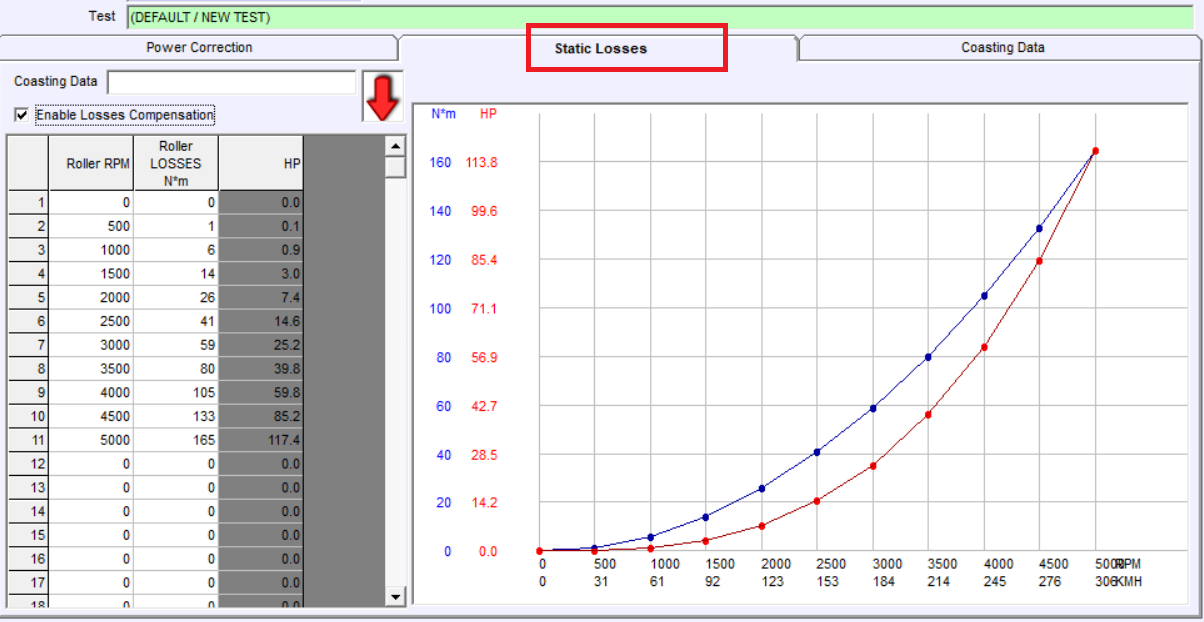
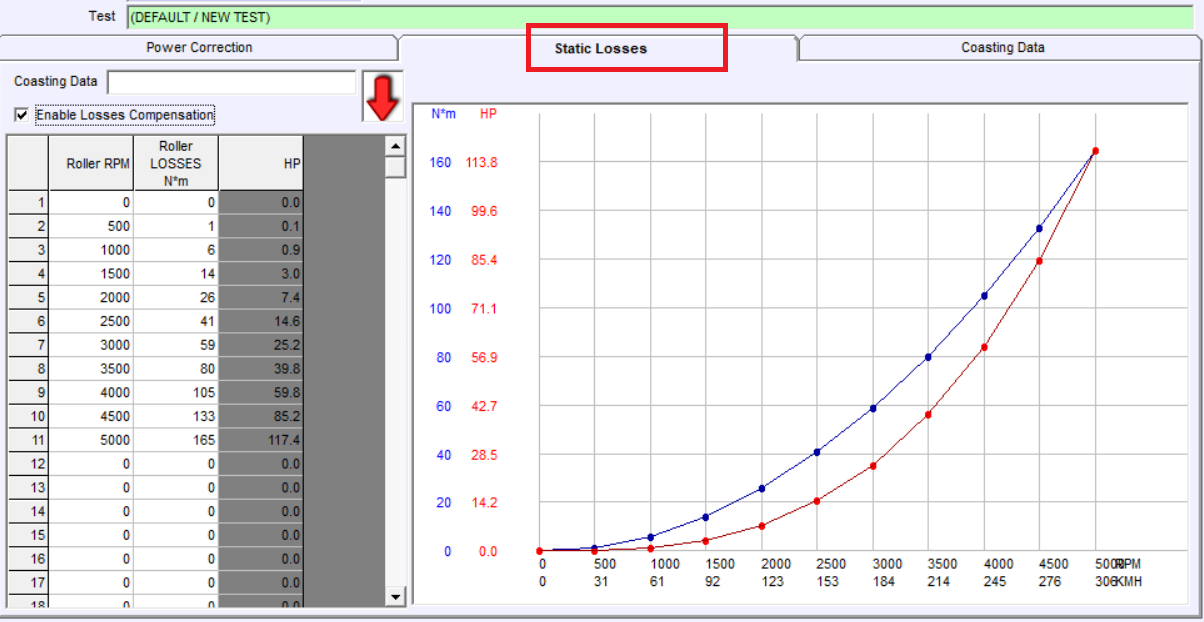
Inertial tests: it is common that the longer the test (higher gear) the more power that the engine can develop, this happens for two reasons:
- Engine Inertia (which is unknown) causes that part of the power is used for accelerating the engine itself. For higher gears the most of the power is used to accelerate the rollers, and as the gear becomes lower the amount of power for accelerating the engine is higher. This maximum happens at first gear (in some engines it could be even about 50%), and of course at Neutral position it is 100%
- If it is a turbocharged engine, the time that the turbo has for reaching its top pressure is lower in lower gears than it higher gears
Braked tests: Both issues are considerably attenuated when performing braked tests of a same duration.
Additionally, In twin roller dynos there is also another source of differences, which is the tyre deformation: normally the lower the gear the higher the pressure that the tyre does against the front roller and the higher the losses, but these losses cannot be measured in the coast down phase. Then my recommendation is using the higher gear possible in these dynos, and even increase the tyre pressure to reduce the deformation (but if you see that slippage increases then you should reach a balance)
example of tyre deformation
Sure!. The general rule for the Low-Pass-Filter (the one that is set in seconds) is that the filter size shouldn’t be bigger than the test duration / 10 (the acceleration part).
As a general rule an inertial dynamometer shouldn’t produce acceleration tests of less than 5 seconds (at the suitable gear), then the minimum filter you should be able to use always is 0.5 s.
For braked dynos as you are able to control the test duration with the brake, our recomendation is having tests between 7 and 10 seconds (or more), then the filter could be 0.7 to 1.0.
On the other hand the filter named “HF” normally is used with fixed values. Actually all filters are low pass type, but the “HF” attenuates specially higher frequencies, (actually it is a Low Pass Filter that focus on higher frequencies), and not so on slow vibrations, for that reason the “Low Pass Filter” was provided to reach lower and lower mechanical frequencies that are present specially in car dynamometers, also the LPF works worse for the very high frequencies, for this reason it is good to use both: “HF” with a fixed value, and LPF depending on the average test size
The recommended values for the “HF” are 5 and 7. The software provides a feedback of the cut frequency, but it is not very intuitive to understand how the test works as frequencies (for instance a “round” HP graph that last 10 seconds has a main componen of a 0.25 Hz wave), for that reason we suggest to use fixed low values (5 to 7)
The problem with the “HF” filter is that the bigger it gets the more delays and distortion it adds, so it is better to use it only for high frequencies (from digital noise and gear teeth irregularities) and not trying to go beyond on filtering, and then using the “LPF” for the mechanical vibrations
In most cases we need to know an estimation of the Power at Engine, which implies to record the coast down phase: friction losses from tyre losses and air-pump losses from brake mainly. This coast down phase must be recorded with the clutch pressed or the Neutral position selected
- Open Gauges Window
- Configure the test:
- Enter data: Vehicle and Customer.
- Mode: Inertial or ramp,
- Starting RPM and ending RPM (for instance 2000 to 6000 RPM), also test duration for ramp test (for instance 10 to 15 sec). Important the ending RPM must be slighly lower than actual value, for instance if the engine reaches 7500 we could set 7000 as top rpm, and the SW will allow us to continue up to 7500 if we want to.
- Stopping mode: normally “Stop When Lower” mode, so the CLUTCH message is shown and the coast down phase is recorded
- Calibrate the ratio: (check the Ratio calibration topic)
- Press “continue” or the start/stop button to enter the semaphore window
- Prepare the vehicle at a speed below the starting RPM
- Open full throttle. If in ramp mode, wait until the pre-load and stabilisation ends
- The test will start automatically
- When ending RPM is reached, the clutch message will be displayed, but the user can continue accelerating if the engine top speed has not been reached
- Press the clutch / Enter Neutral and wait until the recording ends
- The test will stop automatically when speed is below the point set at configuration (by default 50% between starting speed and ending speed)
Important: the software only uses the Roller Channel for all calculations related to the engine (Transformation from Roller Engine scale to Torque at Engine, and Calc RPM for Graph’s Engine RPM axis). This is done in this way for two reasons:
- because some engines cannot always provide Engine RPM readings, for instance diesel engines or engines based on pressured air, or others, and
- because the engine RPM Channel is often a problematic channel, specially in multi-cylinder engines. Only when the Engine RPM channel is read from an ECU the data can be 100% reliable For this reason the software is based on the calibration of Ratio value, which is the relationship between Engine RPM / Roller RPM. For instance if the engine is running at 3000 rpm while the rollers are running at 1000 rpm then the ratio will be 3.0
How to calibrate the ratio:
There are five options:
- Using RPM clamp, when using any of the clamps, or in general the Engine RPM TTL input (for instance from the ECU) the software will be updating the ratio value while the vehicle accelerates at the Gauges Window, or also after the first run.
How to use it:
- the user should engage the gear that is going to be used for the test,
- then accelerate progressively and the SW will be updating the ratio value while the acceleration persists,
- then when the ratio value is stable, the ”Update” button can be disabled to block this value, or the mode can be set to Fixed Ratio, so it does not change anymore.
- Then the test can be started as usual either using the start and stop RPM values (this works for inertial and ramp tests).
On the other hand, if the ratio was not calibrated before starting the test, even despite that SW can calculate the correct Ratio value after the test is done, the starting and ending RPM values shouldn’t be used because they will cause random starting and ending points. Alternatives:
-
- Use either manual start/stop (only for inertial)
- Use start and stop referenced to SPEED
- Use OBDII, ECU or XDS data. This method works in the same way that the option 1 (clamp): the SW updates the ratio while the vehicle accelerates at the Gauges window, but the main difference is that the source of Engine RPM value is not the Engine RPM Channel (0x31) but the OBDII/CAN/ECU channel 0x91. The rest of the operation is the same. This external source can be also used at the Manual Calibration Window.
- Fixed Ratio. This is not an actual calibration method, but a mode to keep the latest determined value fixed once it has been determined by other methods
- Manual Ratio Calibration. When there is no way to measure the actual RPM, or the user don’t want to spend time connecting clamps, interfaces or whatever, the SW still is able to find the ratio using the vehicle’s tacho in a visual way. The procedure is simple:
- Open the Ratio Calibration Window (button or CTRL+F7)
- Set a RPM reference. Typically aprox of top rpm /2, for a diesel engine a typical value would be 2000 rpm, and for a petrol engine 3000-4000 rpm depending on the engine
- Accelerate using the gear which will be used for the test until the engine reaches the previously set reference (2000, 3000, 4000…)
- and then click on “Continue” or use the start/stop switch (when it is installed). The software will use the reference and the current roller speed to determine the ratio. For instance reference is 3000 rpm and roller is 1000 rpm, the ratio = 3.0
Note that the OBDII/CAN data can be used here too, the main difference is that the user will not need to be so accurate to set the engine to the exact speed that the reference points, because the reference will be updating in real time, thus if the engine is running at 3050 rpm instead of 3000 rpm it will not be important because the reference will be also 3050.
- Ratio manual calculation, based on gearbox and transmission calculations
In the standard version 1.2, only Left and Right buttons are “software” buttons, Then the program can implement several functions (menus, etc) depending on the context, while up, center and down are “hardware/firmware”: the DAQ will perform a fixed function even if the computer is not runing, but that prevents to add more functions depending on the context, specially the menu handling (using the left key all time) is a bit counter intuitive
In the new version 1.3 all buttons are “software” type, then the program can implement several functions depending on the context.
now Up and Dn buttons will perform different functions depending on the mode: Steady rpm up/dn, brake up/dn, etc. But when the menu is visible then will move the current selection up and down, which is more intuitive. Also the left button can be configured in the software for the Cancel function (equivalent to ESC key) or other function like fixed braking (20% or other value) without entering the “Panic” condition. But this is under test now
The idea is that as they are all “software” type they could have more complex functions in the future


Road Simulation is an ADVANCED mode, which is more intended for WLTP cycle, than for testing. Indeed Road Simulation is a kind of modified RAMP which uses a mathematical model to simulate what the vehicle should do in the road according to the instant output the vehicle performs
Users that want to use Road Simulation because they didn’t configure the Ramp correctly will not have a better response with Road Simulation because it is indeed a more complex mode and needs more configuration
Road simulation is easier to be used in rolling road dynos and hub dynos (with automatic gearbox vehicles) than with engine dynos due to the lack of inertia of engine dynos.
Road Simulation is based on three coefficients (C, B, A) to simulate the road and wind-drag load, and a weight value to simulate the inertia of the vehicle.
C is the square term of the polynom and simulates mainly the air force which increases as a square function with speed. Please note that C is not the vehicle’s Cx, but A (frontal surface) by Cx by other constants (see the formula below)
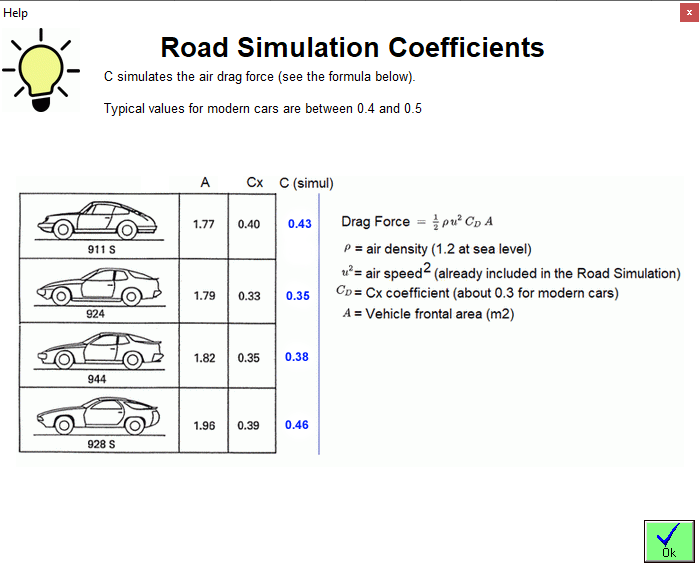
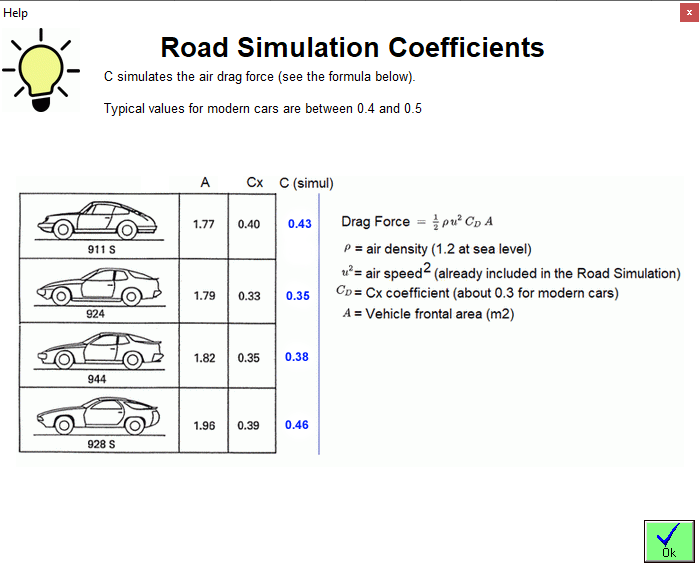
B and A are the linear and constant coefficients in the polynom which mainly simulate the tire friction and slope
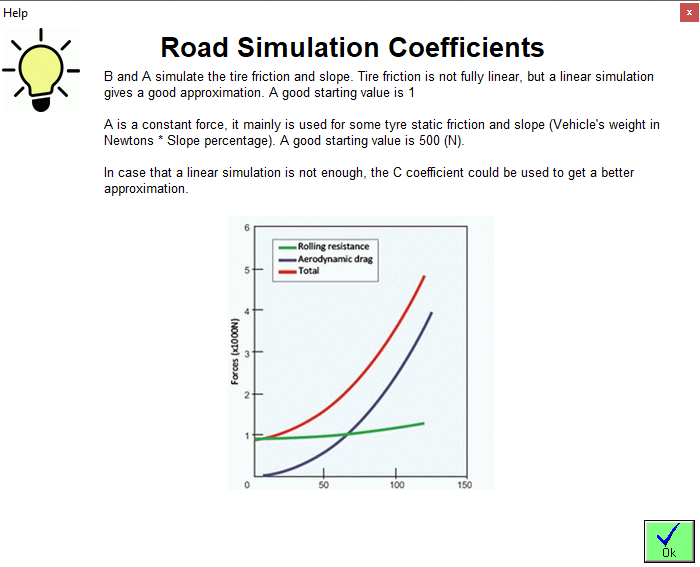
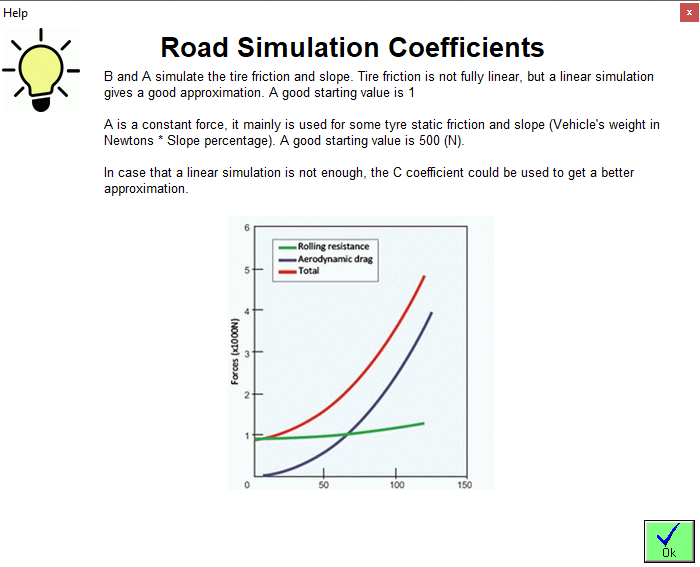
Finally the simulated mass is the vehicle’s mass. If the value entered in this field is lower than the equivalent mass of the dyno the simulation will be performed with the dyno equivalent mass, as there is no way (with braked dynos) to accelerate the vehicle to simulate a lower mass (only dynos with electric motors may reach this feature)
It is not a simple task to configure it. You can start with C=0.40, B=1, A=0 and perform several tests. The goal is that the top speed is the same in the dyno as in the road, and that acceleration times are the same. There are advanced procedures to measure those coefficients, but it is not the purpose of this brief explanation.
Additionally there are other coefficients to improve the Road Simulation


Max acceleration (roller), if it is higher than 0, it limits the maximum acceleration to avoid unexpected behaviour on low inertia dynos
Road Simulation PID: it provides an alternative PID to the main PID used for Steady and Ramp modes, as normally we need a more reactive PID (higher KP, about +50% than the normal KP) in order to provide a better speed tracking in the Road Simulation mode, as the priority is the speed profile, not the power measurement
As alternatives to Ramp and R/S modes (if the PID does not provide the desired results) the user can use the Fixed Brake or Brake Map modes, but they only will work correctly on high inertia dynos (rolling road dynos) as the residual torque (engine torque – brake torque) is very critical on low inertia dynos (hub dynos and engine dynos). In this case only PID modes should be used. A special exception to this case is when testing electric motors in a “reverse test mode” as the motor starts from top speed, then the brake increases its torque progressively until the motor stalls, the motor normally is very stable during all the process regardless the dyno inertia because the motor torque map normally is decreasing with speed, but this does not apply to normal ICE engines because once the TQ peak is reached (say 2000 rpm at a diesel engine) the engine becomes totally unstable and stalls.
Dyno Design
Despite theis higher complexity and cost, typically braked dynos use Hollow Rollers because the capacity of having longer axles, which are necessary for connecting the rollers between them (car dynos) and with the brake. Car dynamometers can also use hollow rollers for inertial dynos because it is necessary to connect them in pairs.
Advantages of hollow rollers:
- they don’t need dynamic balancing in most cases
- they are easier to build (despite the amount of job to machine de axles)
- they are easy to calculate. Using our spreadsheet you can get the inertia (MOI) using only the diameter and width (without axles)
Disadvantages of solid rollers:
Advantages of hollow rollers:
- They have long axles, which is necessary for braked dynamometers
- They are more efficient with respect their weight, typically 85% to 90% of the mass work as inertia
Disadvantages of hollow rollers:
- They are more complex to build and need to be perfectly dynamically balanced
- They are normally more costly
- They are difficult to calculate if you don’t have the exact sizes
Spreadsheet for calculations:
http://www.sportdevices.com/download/rollerssheet.xls
Typically we use solid rollers for inertial dynamometers, specially for Motorcycle dynamometers due to its extreme simplicity. They can be used for car dynamometers although the amount of steel to be removed to create longer axles (in order to connect each side roller) may be a bit high, which makes more time and money costly the task of creating those axles
Advantages of solid rollers:
- they don’t need dynamic balancing in most cases
- they are easier to build (despite the amount of job to machine de axles)
- they are easy to calculate. Using our spreadsheet you can get the inertia (MOI) using only the diameter and width (without axles)
Disadvantages of solid rollers:
- They are normally heavier than hollow rollers, but only 1/2 of the mass works as inertia, While a hollow roller normally is in the 85% to 90% range.
- They need more amount of steel, although it is not specially expensive compared with the additional tasks to build and balance a hollow roller
- Normally they have short axles, which makes more difficult to add extra parts: disk brakes, couplers for a future brake, etc
Inertia (MOI) calculation:
MOI = (Diameter/2) ^4 * PI (3,1416) * Lenght (m) * ρ (density of steel = 7900 kg*m3) / 2 (ALL sizes in METERS!)
For instance for a 320D x 480W roller, MOI = (0.320/2)^4 * 3.1416 * 0.480 (m) * 7900/2 = 3.9 kg*m2
And weight (not used for power calculation) = (Diameter/2)^2 * PI * Length (m) * ρ (density of steel) = (0.320/2)^2 * 3.1416 * 0.480 * 7900 = 304.9 kg (without axles)
Roller example:
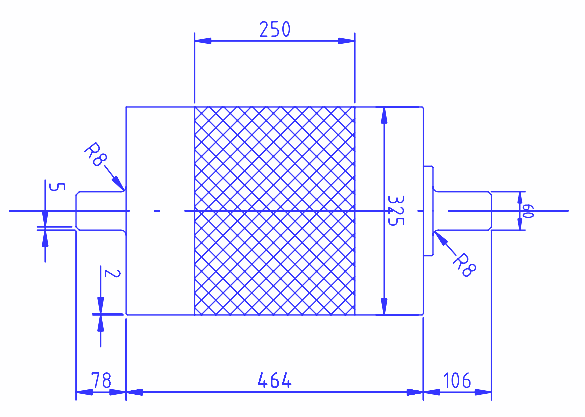
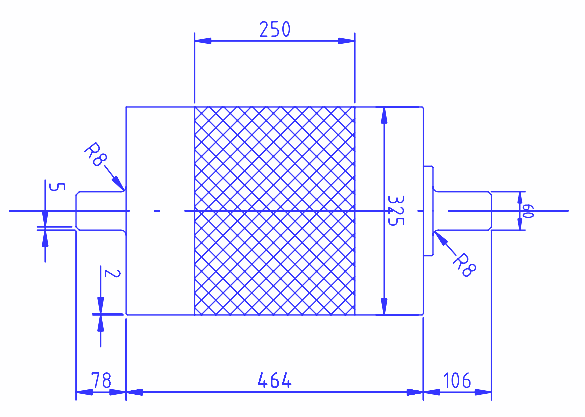
http://www.sportdevices.com/download/plans/Dyno325roller.pdf
Spreadsheet for calculations:
http://www.sportdevices.com/download/rollerssheet.xls
In most Braked dynamometers, the brake is installed over bearings and only the load cell prevents it to turn. Then the brake torque is converted to a linear force in the load cell as a result of the TQ / Lever (meters) formula. Note that torque can run in both directions, but normally we would use the load cell in compression mode,
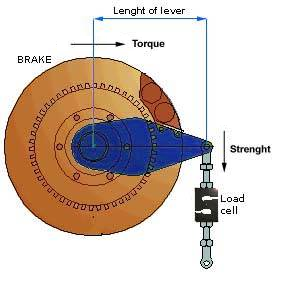
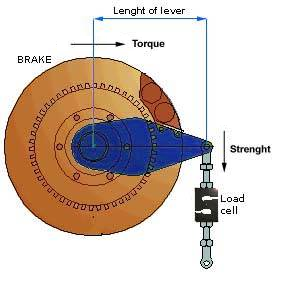
Then, for instance, for a 1700 Nm brake and a 300 mm lever (distance from brake AXLE to load cell), the max force received in the cell will be:
1700 (Nm) / 0.300 (m) = 5666.n (N) –> (divided by 9.8 or 10) –> 578 Kg
In some cases a 500 kg load cell could be ok for this case, but if you expect to test high power cars then the rated 500 kg may be overpassed often and then it will better to choose a 1000 kg load cell.
Common Issues
Windows can eventually detect a high data stream from the DAQ (and previously from the Weather Station) and decide that it is a MOUSE, it will install the Ballpoint Drivers and will block the access from other applications. The cursor in the screen can become crazy as it will interpret the data from the DAQ as mouse movement.
Solution:
- Turn the DAQ OFF, or disconnect the USB from the computer
- Manual: Open the Windows Device Manager and DISABLE the Ballpoint device (do not uninstall it, Windows would install it automatically again)
- Automatic: Execute Sportdyno in Admin mode to give the application Admin rights (note that it does not mean to log with an Admin user). Execute the “Options/Disable Ballpoint” menu option. Note: it will only work with Admin rights.
Manual Method:
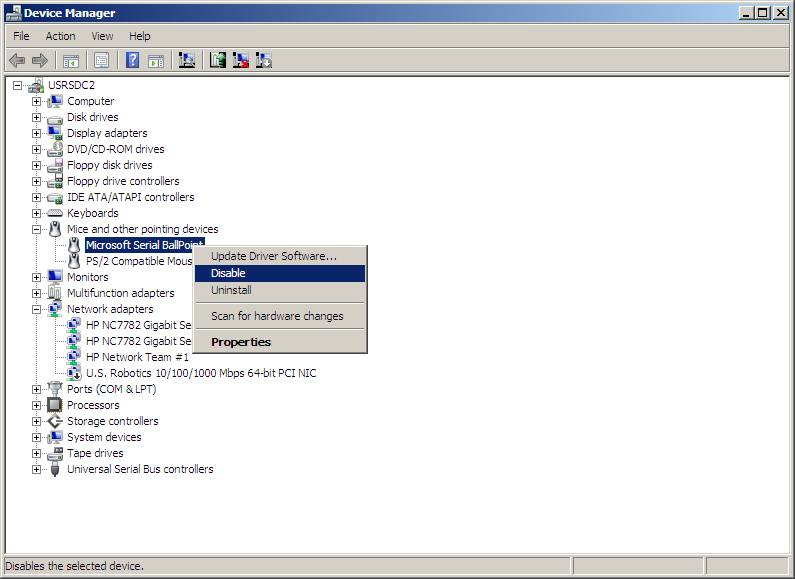
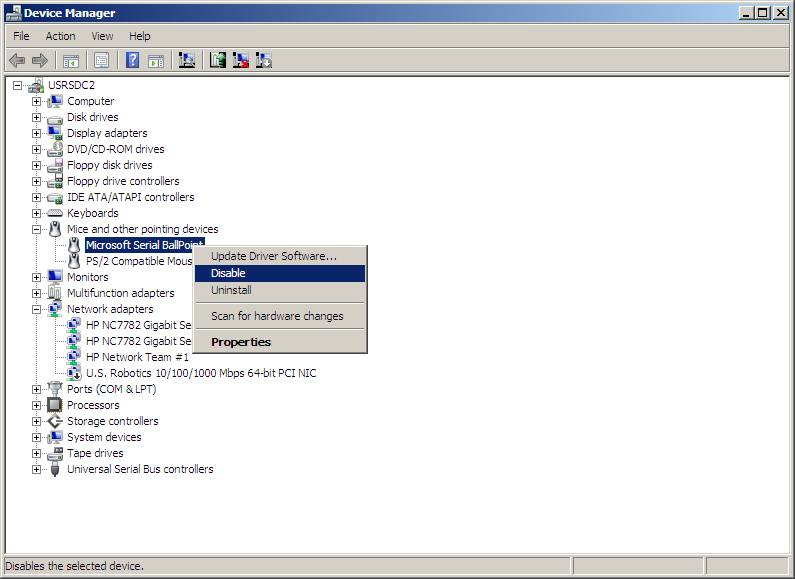
Automatic Method:
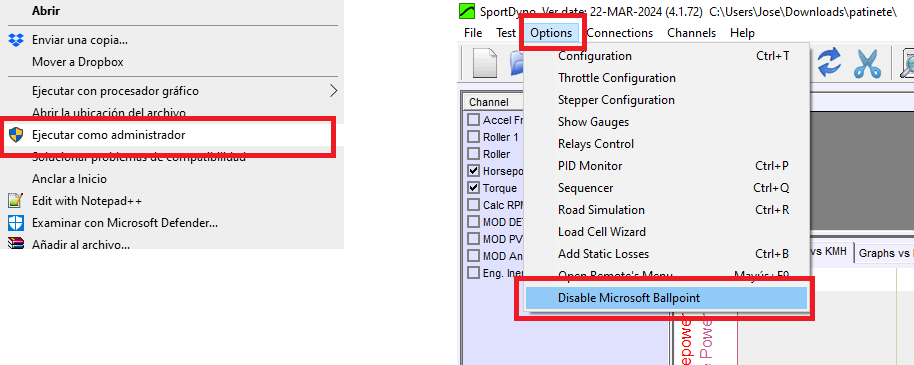
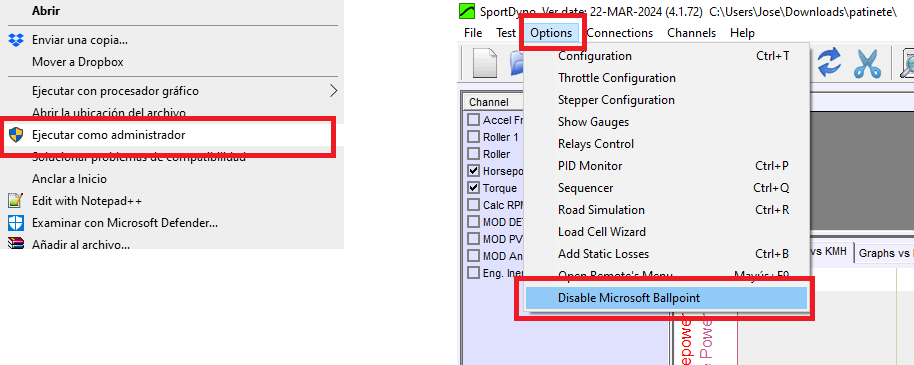
Note that for this verification we are using the default “New Lambda (10-18AFR)” type for AN1 / LAMBDA1 channel


Verifying the Heating Up phase
The controller will provide 2 different voltages / outputs for the heating-up and steady phases
- During the first seconds, the controller is in the heating-up phase and will output aprox 2.5V in the output, 14 AFR in the software.
- Once the lambda has reached its working temperature at free air, it will output 5V or 18 AFR (aprox). The sensor should be hot, be careful if touching it
Possible issues:
· The lambda is not physically hot: Check that the voltage provided by the small 12V power supply is stable at 12V with a multimeter (with the controller and the lambda connected).
-
- If the voltage is low then the power supply could be faulty
- If the voltage is 12V normally means that the controller is faulty
- The lambda is hot, but the output stays at 2.5V / 14 AFR, normally this means that the controller is faulty, but check it with another lambda sensor if possible
Verifying the Operating phase
- Apply gas from a lighter (no flame) directly in the lambda sensor orifice, the output should go low fast: 0V / 10 AFR
- Remove the lighter and allow the gas to disipate (or blow the sensor to make it faster), the output should go back to 5V / 18 AFR
Note: if you are having issues with the connection to the DAQ and the software, the voltages can be directly verified in the 6 pin connector from the Lambda Controller at pin 4 (signal) vs pin 5 GND, or at the square plastic connector (check the wires colours in the controller)
During the installation / setup process it is common that some settings are not correct which can lead to ‘absurd’ readings (very high or very low). It is important to do this check list:
- Number of Pulses and Prescaler (a little error in the number of teeth or prescaler usually gives huge errors in the power readings)
- SP1/SP4: please verify the number of teeth and prescaler. Plase read this link: https://sportdevices.com/ufaq/sp1-configuration-inertial-tests ). Also a bad SP1 synchronization can give strange results
- SP1+/SP5/SP6: Software Prescaler is always 1 (except when using High Pulses Encoders and the internal Hardware prescaler, but it is an internal setting)
- Inertia / MOI (a little error here has a little impact in the output)
- Solid roller it is easy to calculate the inertia, please check our spread sheet: http://www.sportdevices.com/download/rollerssheet.xls
- Hollow roller: here the difficulty is to know the internal thickness of the cylinder and the walls. You can check our double-ramp calibration/estimation doc: http://www.sportdevices.com/download/manuals/Double%20Ramp%20Test.pdf
- Load Cell Calibration (when applicable) https://sportdevices.com/ufaq/load-cell-calibration/
- The Test Procedure itself: For Engine Power Measurement it is important to record correctly both phases: acceleration at full throttle and coast down in neutral or clutch pressed (when possible). If the coast down phase has not been recorded it is easy that 20% or more friction losses have not been recorded, then the output will be low
- Power Transmission Correction. In most cases use a value of at least 10% (there are very small engines that need 7%, but most are over 10%). There are other exceptions like electric hub motors (direct traction) and similar which will use correction=0%
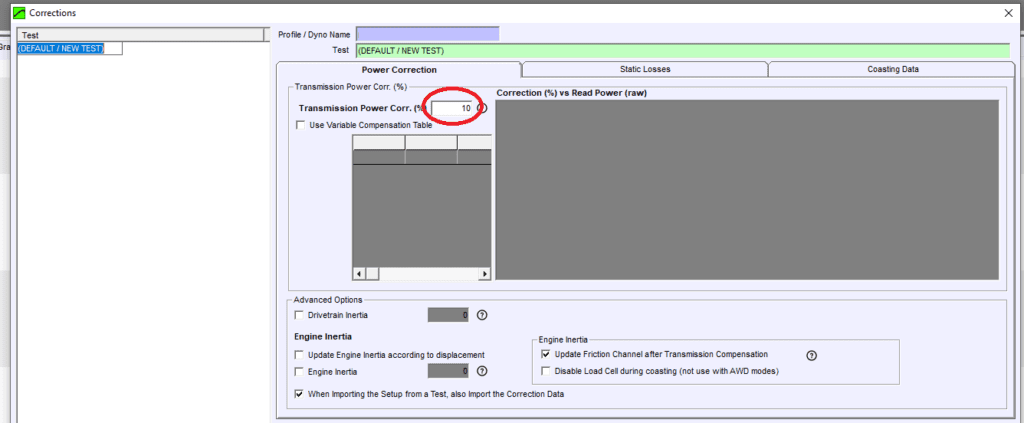
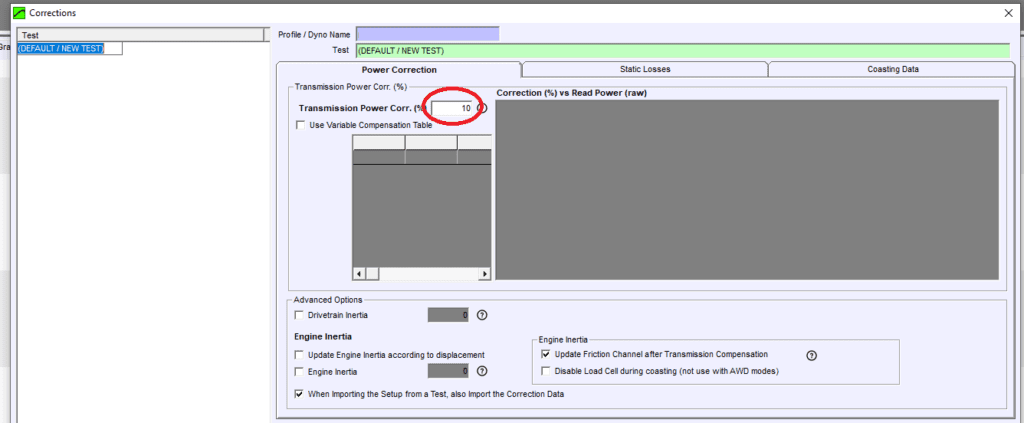
After the installation:
It may exist differences specially in high power cars and specially on twin roller dynos
High Power Cars may need a higher ‘power transmission correction’ value, but it is difficult to anticipate it. There is a function that assigns a value from a table, but this table may change change with each car and each dyno
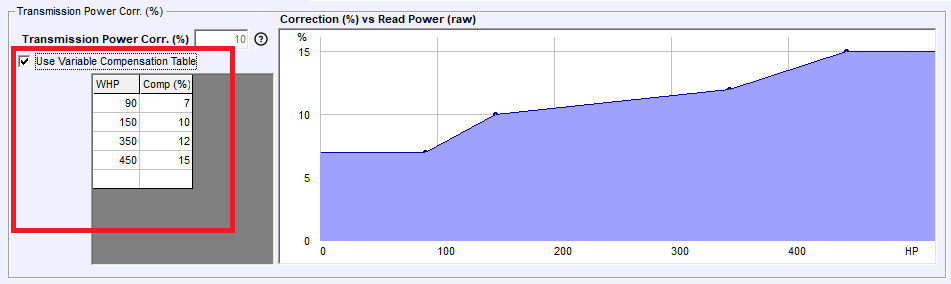
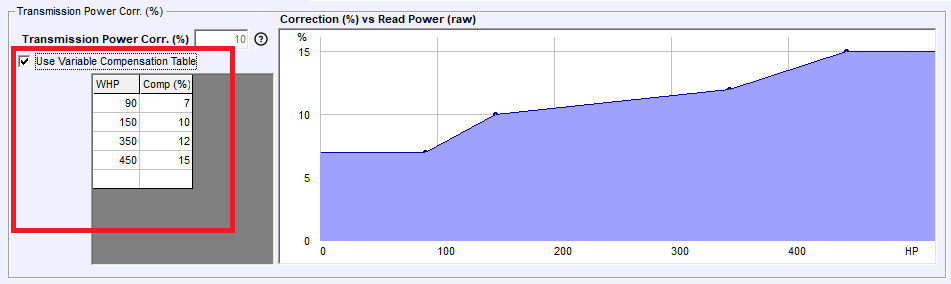
Twin roller dynos are specially complicated with high power cars, even worse if the rollers are more separated. In twin roller dynos there is also another source of differences, which is the tyre deformation: normally the lower the gear the higher the pressure that the tyre does against the front roller and the higher the losses, but these losses cannot be measured in the coast down phase. Then the recommendation is using the higher gear possible in these dynos, and even increase the tyre pressure to reduce the deformation (but if you see that slippage increases then you should reach a balance)
example of tyre deformation
The provided USB-RS232 adapter has a default latency which results too slow for realtime data displaying. It does not affect to the recording but makes the visualization very slow.
There are two options:
- Use the “FTDI (0xnn)” port. When using the FTDI port the software can use the FTDI drive for selecting automatically the latency to 1 ms, which is the easiest way. (see below)
- Configure manually the COM latency to 1 ms (see below). This is recommended only for advanced users.
FTDI Port


Manually setting the COM Latency to 1 ms (advanced)
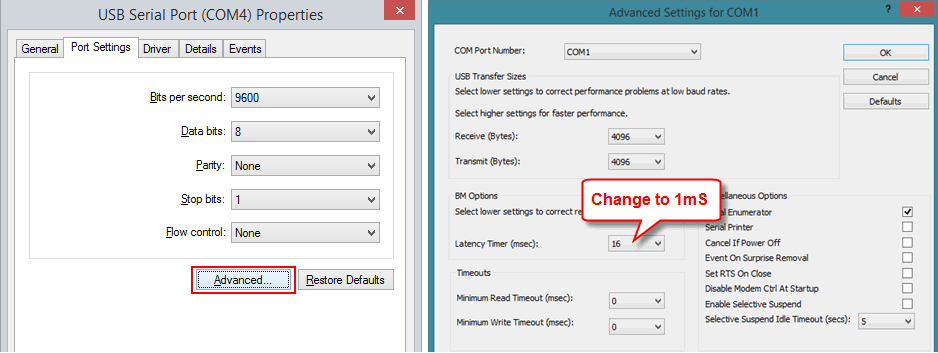
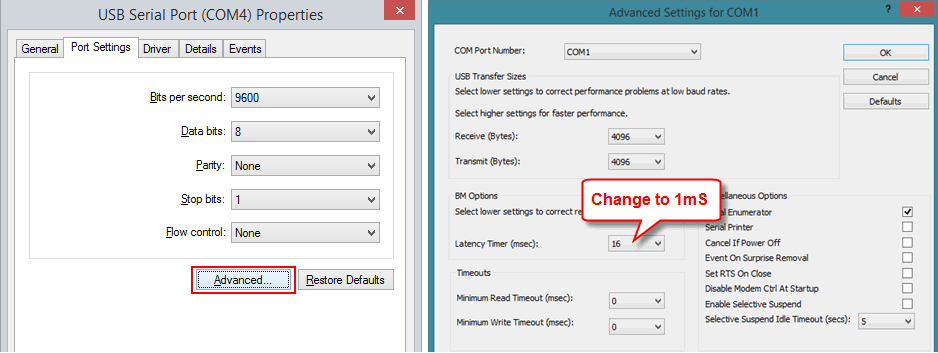
Something that causes many misunderstandings to new users regarding the SP1 configuration is the confguration of number of teeth and prescaler due to the fact that the SP1 does not syncrhonize these settings with the PC (the SP1 will not send this information during the connection process and then the PC will not be able to synchronize it). Then it is necessary:
- Ensure that the connection between the PC and the SP1 is established before configure these settings
- Configure the Number of Teeth and prescaler. For our stock gear it is Teeth=16 and Prescaler=1 (in most cases). Note that this configuration is only valid for rollers over 320 mm and max speed below 225 km/h! (max roller speed 3750 rpm). For higher speeds use the “auto” setting, which will set the prescaler to 4 to avoid problems. Please check the table below
- Press the “disquette” button, or press OK and reply “YES” to the question “do you want to send the new settings?”
- Verify that the SP1 LCD shows the stored value (this lasts only 2 or 3 seconds)
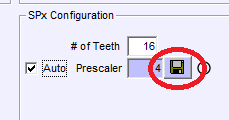
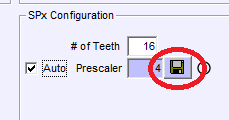
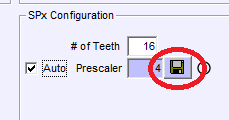
** Note: we are testing a new firmware which implements the same synchronization as SP1+, SP5 and SP6. This FW could be used in all SP1 V4 units
AUTOMATIC Prescaler Selection:
When the “auto” setting is ON, the software will select
- Teeth: 1 to 12: prescaler = 1
- Teeth: 13 to 49: prescaler = 4 (note that for our stock 16T gear it will chose prescaler=4, which can reduce the accuracy at low speeds)
- Teeth: 50 or more: prescaler = 16
Manual Prescaler Selection
In general when SP1 is used with our stock 16T gear, number of Teeth = 16 and prescaler = 1, but only for rollers over 320 mm diameter and top speed below 225 km/h. For lower diameters or higher speeds prescaler should be 4
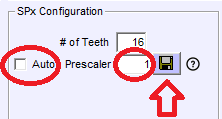
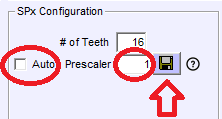
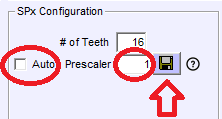
As maximum SP1 input is 1000 pulses per second, the user should ensure that the top frequency is not overpassed using the following formula:
Max Freq = Max Roller RPM / 60 * Teeth / prescaler
(Max Roller RPM = Max Speed (km/h) / 3.6 / (diameter_mm / 1000) * 3.1416) * 60)
Example:
For instance for a 320 mm roller running Max Roller RPM at 225 km/h is: Max Roller RPM = 225 / 3.6 / (0.320 * 3.1416) * 60 = 3730 RPM
And for 16T and prescaler = 1 Max Freq = 3730 / 60 * 16 / 1 = 994 Hz
Then for higher speeds (over 225 kmh) or lower roller diameters (below 320 mm) the prescaler should be 4 as in the automatic mode.
For the rest of combinations, say teeth 80 normally there is no need to do any calculation. The 16T is a little more problematic because it is in the border between prescaler=1 and prescaler=4, but it was selected as stock gear because it provides more pulses for the braked dynamometers.
There are two possible causes:
Bad ratio or slip / tyre deformation: Check the actual engine RPM channel or OBDII RPM channel vs Calculated RPM to see if the actual RPM gets far from the calculated RPM graph, specially in the middle section (due to the higher torque)
Excessive filtering: Max recommended filter (LPF: Low Pass Filter) is 1/10 of the test duration (acceleration phase). For instance a test of 8 seconds (acceleration) should use a maximum filter of 0.8s. Tests which use excessive filtering (for instance LPF=4.0 sec) will show the power graph excessive rounded and will show lower HP and TQ results. This can also affect to the top calculated RPM values