Dyno Design
Despite theis higher complexity and cost, typically braked dynos use Hollow Rollers because the capacity of having longer axles, which are necessary for connecting the rollers between them (car dynos) and with the brake. Car dynamometers can also use hollow rollers for inertial dynos because it is necessary to connect them in pairs.
Advantages of hollow rollers:
- they don’t need dynamic balancing in most cases
- they are easier to build (despite the amount of job to machine de axles)
- they are easy to calculate. Using our spreadsheet you can get the inertia (MOI) using only the diameter and width (without axles)
Disadvantages of solid rollers:
Advantages of hollow rollers:
- They have long axles, which is necessary for braked dynamometers
- They are more efficient with respect their weight, typically 85% to 90% of the mass work as inertia
Disadvantages of hollow rollers:
- They are more complex to build and need to be perfectly dynamically balanced
- They are normally more costly
- They are difficult to calculate if you don’t have the exact sizes
Spreadsheet for calculations:
http://www.sportdevices.com/download/rollerssheet.xls
Typically we use solid rollers for inertial dynamometers, specially for Motorcycle dynamometers due to its extreme simplicity. They can be used for car dynamometers although the amount of steel to be removed to create longer axles (in order to connect each side roller) may be a bit high, which makes more time and money costly the task of creating those axles
Advantages of solid rollers:
- they don’t need dynamic balancing in most cases
- they are easier to build (despite the amount of job to machine de axles)
- they are easy to calculate. Using our spreadsheet you can get the inertia (MOI) using only the diameter and width (without axles)
Disadvantages of solid rollers:
- They are normally heavier than hollow rollers, but only 1/2 of the mass works as inertia, While a hollow roller normally is in the 85% to 90% range.
- They need more amount of steel, although it is not specially expensive compared with the additional tasks to build and balance a hollow roller
- Normally they have short axles, which makes more difficult to add extra parts: disk brakes, couplers for a future brake, etc
Inertia (MOI) calculation:
MOI = (Diameter/2) ^4 * PI (3,1416) * Lenght (m) * ρ (density of steel = 7900 kg*m3) / 2 (ALL sizes in METERS!)
For instance for a 320D x 480W roller, MOI = (0.320/2)^4 * 3.1416 * 0.480 (m) * 7900/2 = 3.9 kg*m2
And weight (not used for power calculation) = (Diameter/2)^2 * PI * Length (m) * ρ (density of steel) = (0.320/2)^2 * 3.1416 * 0.480 * 7900 = 304.9 kg (without axles)
Roller example:
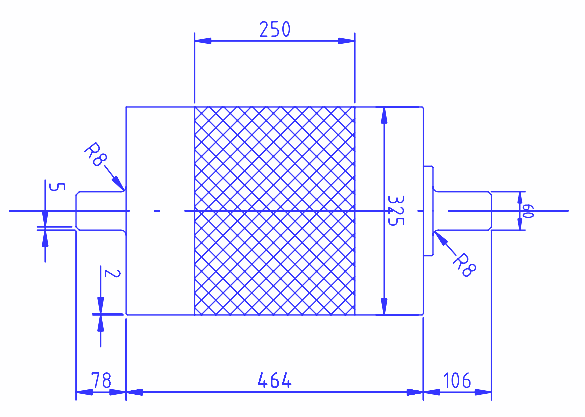
http://www.sportdevices.com/download/plans/Dyno325roller.pdf
Spreadsheet for calculations:
http://www.sportdevices.com/download/rollerssheet.xls
In most Braked dynamometers, the brake is installed over bearings and only the load cell prevents it to turn. Then the brake torque is converted to a linear force in the load cell as a result of the TQ / Lever (meters) formula. Note that torque can run in both directions, but normally we would use the load cell in compression mode,
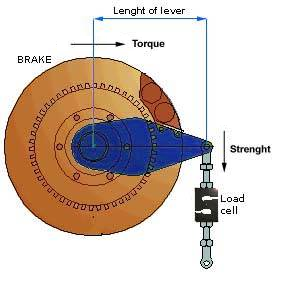
Then, for instance, for a 1700 Nm brake and a 300 mm lever (distance from brake AXLE to load cell), the max force received in the cell will be:
1700 (Nm) / 0.300 (m) = 5666.n (N) –> (divided by 9.8 or 10) –> 578 Kg
In some cases a 500 kg load cell could be ok for this case, but if you expect to test high power cars then the rated 500 kg may be overpassed often and then it will better to choose a 1000 kg load cell.