During the installation / setup process it is common that some settings are not correct which can lead to ‘absurd’ readings (very high or very low). It is important to do this check list:
- Number of Pulses and Prescaler (a little error in the number of teeth or prescaler usually gives huge errors in the power readings)
- SP1/SP4: please verify the number of teeth and prescaler. Plase read this link: https://sportdevices.com/ufaq/sp1-configuration-inertial-tests ). Also a bad SP1 synchronization can give strange results
- SP1+/SP5/SP6: Software Prescaler is always 1 (except when using High Pulses Encoders and the internal Hardware prescaler, but it is an internal setting)
- Inertia / MOI (a little error here has a little impact in the output)
- Solid roller it is easy to calculate the inertia, please check our spread sheet: http://www.sportdevices.com/download/rollerssheet.xls
- Hollow roller: here the difficulty is to know the internal thickness of the cylinder and the walls. You can check our double-ramp calibration/estimation doc: http://www.sportdevices.com/download/manuals/Double%20Ramp%20Test.pdf
- Load Cell Calibration (when applicable) https://sportdevices.com/ufaq/load-cell-calibration/
- The Test Procedure itself: For Engine Power Measurement it is important to record correctly both phases: acceleration at full throttle and coast down in neutral or clutch pressed (when possible). If the coast down phase has not been recorded it is easy that 20% or more friction losses have not been recorded, then the output will be low
- Power Transmission Correction. In most cases use a value of at least 10% (there are very small engines that need 7%, but most are over 10%). There are other exceptions like electric hub motors (direct traction) and similar which will use correction=0%
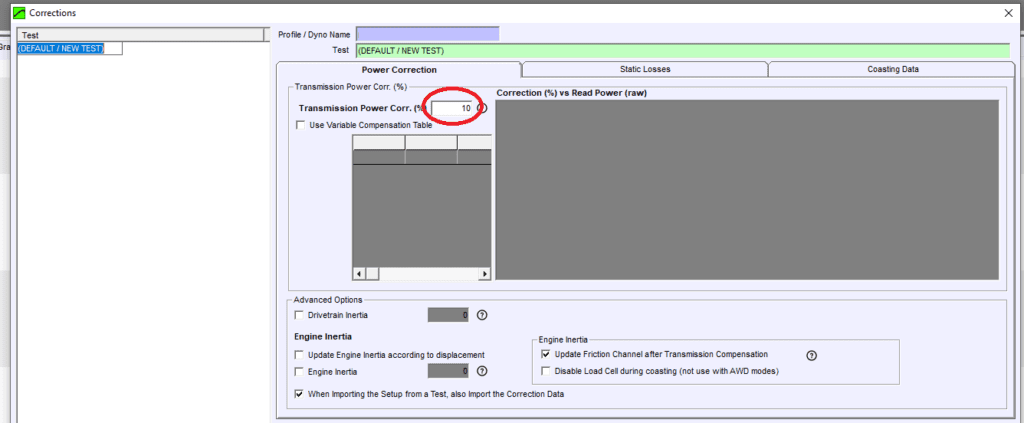
After the installation:
It may exist differences specially in high power cars and specially on twin roller dynos
High Power Cars may need a higher ‘power transmission correction’ value, but it is difficult to anticipate it. There is a function that assigns a value from a table, but this table may change change with each car and each dyno
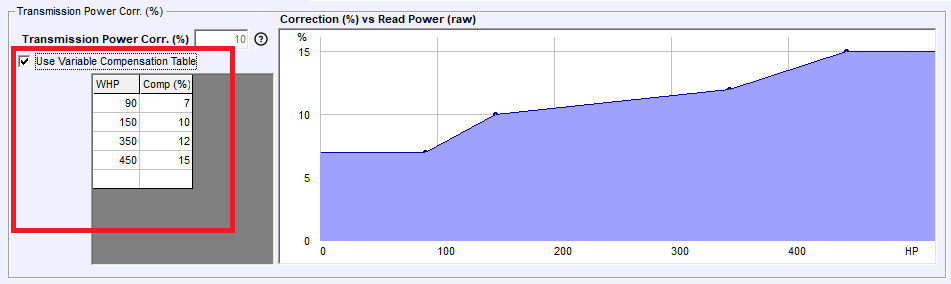
Twin roller dynos are specially complicated with high power cars, even worse if the rollers are more separated. In twin roller dynos there is also another source of differences, which is the tyre deformation: normally the lower the gear the higher the pressure that the tyre does against the front roller and the higher the losses, but these losses cannot be measured in the coast down phase. Then the recommendation is using the higher gear possible in these dynos, and even increase the tyre pressure to reduce the deformation (but if you see that slippage increases then you should reach a balance)
example of tyre deformation